We worked with Schweitzer Engineering Laboratories to improve manufacturing quality and efficiency using visual inspection.
What were the client’s goals?
Schweitzer Engineering Laboratories designs and manufactures industrial control equipment for mission-critical applications in the electric power grid. SEL invests significantly into technology that enables them to manufacture their products with high quality and an extremely low defect rate. They wanted to develop an inspection system that could work in real-time as the product was built, providing instant feedback to assemblers if a portion of the assembly had been installed incorrectly. SEL enlisted EJ Technology Consultants to develop this real-time visual inspection system.
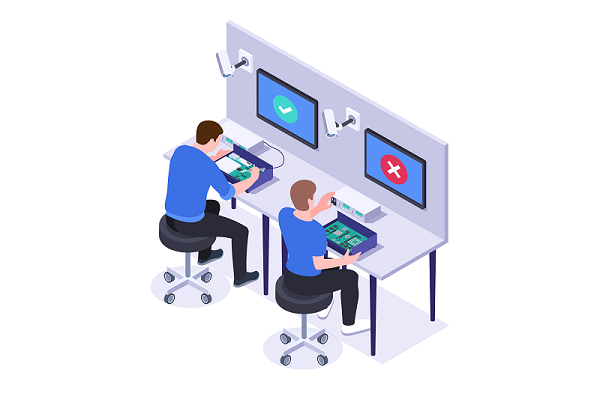
A concept rendering of a visual inspection system for monitoring electronics assembly.
There were several challenges to overcome for the inspection system. The system needed to work even when the assembler’s hands or arms obstructed the camera’s view of the product. It needed to robustly identify defects in a variety of lighting conditions and with the product at different angles and positions. Most importantly, it needed to be cost-effective while remaining fast and accurate enough to significantly reduce the rate of defects.
How did we help?
EJ Technology Consultants assisted SEL in several areas: education, system component selection, and development of the machine learning model and algorithm.
We introduced engineers at SEL to visual machine learning by educating them on how it works, the types of problems it can solve, and the hardware and software required to deploy it for an application. We identified a range of cameras and processors and worked with SEL to downselect to the best options. We also identified a machine learning software framework to use and provided detailed instructions for installing it on their systems.
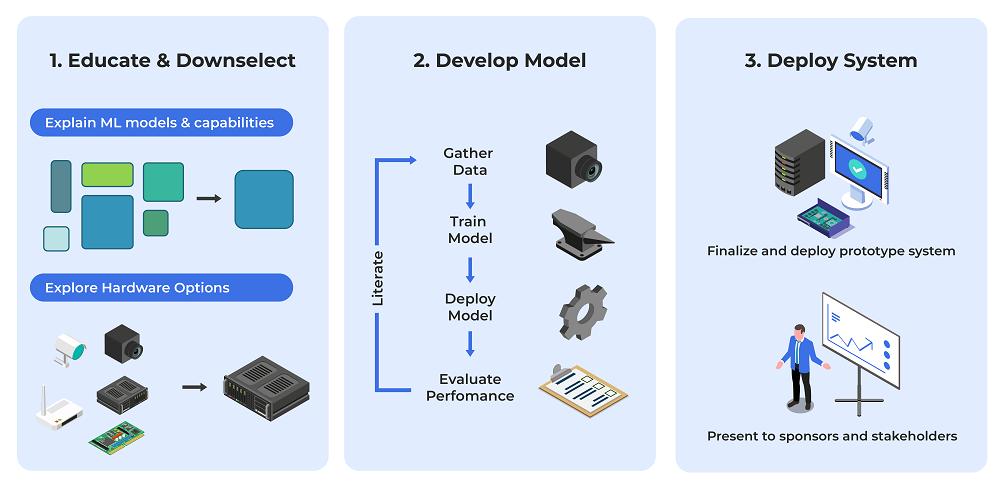
EJTC educated SEL engineers on ML options, developed a model, and deployed the inspection system on-site.
Once the hardware components were ordered, EJTC visited the manufacturing facility to set up cameras at the assembly stations and capture training data. Within two days, we trained a defect detection model and deployed a beta version of the inspection system on their assembly line. During these two days, we collaborated with SEL’s engineers to educate them on each step of the process.
After the on-site visit, EJTC worked with SEL to iteratively improve the visual inspection system by collecting more data, retraining the model, and evaluating its performance in-situ. We investigated and reported on options for improving accuracy across variations in lighting and positioning.
What was the result?
At the end of the project, SEL’s manufacturing innovation department demonstrated the system to high-level management to showcase its potential for improving build efficiency and reducing defect rate. The group received approval and funding to develop the system further and deploy it in other locations on the manufacturing floor.
The engineers on the project gained understanding of the abilities and limitations of using machine learning for visual inspection. They were empowered to continue researching and developing machine learning-based visual applications to solve other problems in manufacturing.